

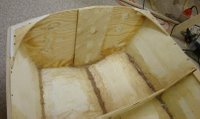
Last night I spent a couple hours finishing up the main rub rails and tracing out the pattern for the middle seat. Earlier, I decided to make my rub rails out of whatever was conveniently available, and in this case it was 8 ft long 1" x 2" strips which I cut down the middle. Because a "1x2" from the store isn't exactly 1" by 2", the new rails ended up being about 3/4" on each side.
I fastened the rub rails to the outside of the 1/4" body with screws. The screws were slightly too long so the tips poked out the other side... I accidentally cut myself last week on one of these little sharp screw tips. So I ground off the tips with a grinder bit and my electric drill.
I also connected two "knees" in the rear of the boat. These "knees" provide some stability and strength to the corners and seams as well as adding a nice aesthetic touch.
~E